Modification of Asphaltic Mixes Using Recycled Vulcanized Rubber Crumb
Jean-Patrick Boussange, master’s student,
Alan Carter, professor,
Michel Vaillancourt, professor École de technologie supérieure
Special collaboration

Worldwide, the most common materials used to build roads are asphalt or bituminous materials because of their favorable viscoelastic properties. These materials are generally a mix of asphalt, granulate material and fillers. Asphalt is by far the most expensive constituent and its cost increases year after year. For example, the cost of PG 58-28 asphalt tripled over the past 9 years: from $245 in 2005 to $740 in 2014. Not surprisingly, contractors are looking for substitutes in order to reduce the percentage of bitumen in their paving formulation.
On the other end, scrap tire disposal has been a problem for many years. In 2003, 290 million tires were dumped in the US and this number is constantly increasing. Practically, these tires are dumped, legally or not, in large stockpiles which often wastes precious land. Recycling tires is becoming a must and companies have developed facilities and processes to break them into crumb rubber.
An obvious solution to both of these problems is to incorporate recycled vulcanized rubber crumb into the asphalt mixture composition. An added benefit is that crumb rubber tends to improve certain properties of the paving compound, while reducing the proportion of asphalt required. For paving contractors, adding recycled crumb rubber means savings on the cost of asphalt and helping to solve the environmental challenge of scrap tires disposal and reducing bitumen consumption. In 2003, 80% of scrap tires were recycled in parallel industries such as construction, industrial energy or pavement and asphalt production.
Several tests have been conducted to assess the impact of incorporating crumb rubber into paving compounds. As a first step, a complete formulation for a conventional ESG-10 asphalt has been prepared and, as a second step, a number of comparative trials have been made with the LC method, using paving compounds modified with various recycled crumb rubber proportions. Three such ESG-10 asphalts containing different percentages of crumb rubber have been formulated.
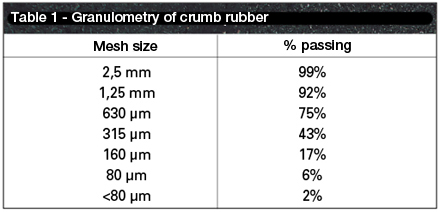
Our main goal for this research project was to formulate an ESG-10 paving compound modified by incorporating tecROAD® recycled rubber directly into the granular material of the paving mix (“dry process”) and optimizing the percentage of asphalt to achieve the desired properties of the paving compound. In fact, tecROAD® contains about 35% of recycled rubber, a formula which has already been successfully tested in Europe to modify asphalt products by adding recycled crumb rubber along with the usual granular material used for paving compound production.
The tecROAD® additive contains recycled rubber particles obtained by a cryogenic fracturing process with a grain size comprised between 0.005 and 5 mm. The detailed granulometry determined in accordance with method LC 26-007 “Analyse granulométrique des granulats d’extraction” recommended by Québec’s Transports Ministry (MTQ) is given in Table 1.
The granulometry of the different ESG-10 remained more or less constant, independently of the proportion of added crumb rubber. The quantity of powder in the mixture was selected on the basis of instructions given by the supplier, UTR Canada inc., the distributor for Canada. Next, an ESG-10 without crumb rubber was prepared using a gyratory shear compactor. In the formulations containing rubber, the quantity of new asphalt had to be adjusted to keep the correct GSC void content. Respective quantities of asphalt and crumb rubber are shown in Table 2.
These paving materials have been subjected to various tests, including rutting tests. Figure 1 illustrates the average results using an LPC rutting tester. As shown on this figure, all paving compounds meet the rutting criteria, but those containing rubber crumbs tend to have a more favorable rutting resistance than the reference material. This is probably due to the presence of the rubber and to a lower asphalt content in these formulations.
Complex modulus measurement tests were made in uniaxial tension-compression, and the results obtained with the 2S2P1D rheology model, are presented as master curves at 30°C. Adding tecROAD® reduces the modulus at high frequency and/or low temperature, which is desirable since it promotes a lesser thermal cracking susceptibility. It should be noted that the modulus tend to be higher at low frequency, or high temperature. This is also a desirable effect since the pavement becomes more rigid at high temperature and this rigidity promotes a better resistance to permanent deformation.
The findings of this study clearly demonstrate that there might be added benefits to the incorporation of tecROAD® rubber crumb into paving pre-mix. The next phase of our project will be to produce paving compounds with tecROAD® rubber for various asphalt grades, in order to study the interactions between asphalt and rubber crumb. It would also be interesting to conduct more tests to ascertain the optimum of added rubber contents and the corresponding optimum asphalt proportion.
The authors want to thank MITACS and Universal Tire Recycling (UTR) for their financial contribution to this project.
Cet article est également publié en français
|