With growing emphasis on Overall Equipment
Sean Chen, Product Manager,
Moxa, Inc.
Special Collaboration
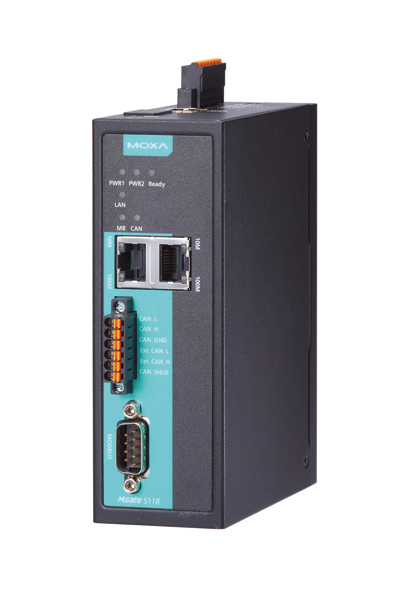
Effectiveness in the heavy-duty vehicle industry, the monitoring of diesel generators has taken on a more significant role in power generation. However, integrating a diesel generator with a large variety of Diesel Generator Monitoring Systems (DGMSs) or programmable logic controllers (PLCs) is easier said than done. Multiple protocols and interfaces, arduous pre-configuration methods, and time-consuming troubleshooting can make life difficult for system integrators regarding integration.
A continuous high-voltage power supply is required to maintain operations in mission-critical applications, such as backup power systems, automatic transfer switches (ATSs), heavy-duty trucks, and tractors. Diesel generators have been widely adopted as power-generation instruments because they are deployed easily at any field site or industrial plant and do not take up much space. Their implementation costs are also very low.
The Importance of DGMS
A DGMS monitors the status of a diesel engine or a diesel generator, tracking the voltage, amperage, RMS, PR, RMO, and other parameters, and will set off an alarm if an engine fails. Additional monitoring functions pertain to the generator’s fuel status, including fuel pressure and fuel consumption especially to alert the control room when thefts occur. PLC systems are also sometimes used to control and monitor diesel generators.
For system integrators, it is vital to find the right protocol gateway to achieve integration as they deal with many different types of DGMSs and PLCs. These systems vary from application to application, country to country, and design to design.
Most diesel generators run the CAN-SAE J1939 protocol, which enables communication and diagnostics among vehicle components, diesel generators, and compression engines, and is suitable for the heavy-duty truck industry and backup power systems at field sites. On the other hand, DGMSs and PLCs employ a number of different protocols. Some DGMSs or PLCs use Modbus, whereas others use Ethernet/IP or PROFIBUS; it all depends on the vendor, the country, and the industry.
Key Considerations
A number of factors need to be considered before setting your sights on a gateway that best fits your purposes. These factors are discussed in detail below:
- Setting J1939 PGN Manually: A diesel generator might have a lot of J1939 Parameter Group Number (PGN) commands, which, depending on the diesel generator, the engineer may need to key in manually. This is a time-consuming operation prone to human error. A well-designed gateway should support a command-learning function, allowing it to learn all the J1939 PGN input commands in only a few steps. Even if many J1939-supported devices are deployed on the same CAN bus, the gateway will be able to recognize each J1939-supported device, with its J1939 commands, individually on the same Control Area Network (CAN) bus. The operational efficiency will be much higher, and the total cost of ownership will be lower.
- Easy Troubleshooting: Field engineers are often unfamiliar with protocol gateways, which to them are essentially third-party devices. They tend to struggle to connect the gateway to the DGMS/PLC correctly since they do not know enough about the communications protocols. A built-in traffic monitor function monitors J1939 protocol traffic, permitting users to monitor the status of the connected CAN devices, including error count, packet count, and bus-offline. The traffic monitor function can also be used to troubleshoot CAN-supported devices. Furthermore, the diagnostic tool helps users check CAN device settings and indicates the availability of CAN devices by reading the J19939 network address.
- A Web Console for Easy Configuration: It is safe to say that most field engineers are knowledgeable about J1939 and know how to set it up, and they may also know enough about DGMSs and PLCs. However, they may not be as familiar with protocol gateways, which are not always easy to set up. The easiest way to set up a gateway is through a web console, making the installation of an additional vendor-provided utility unnecessary. All that is required is a laptop with an Ethernet cable and a web browser to log in to the web page of the protocol gateway.
- A Built-In SD Card Design: Many system integrators can vouch for just how time-consuming it is to configure all the gateways at a site since the configuration process usually involves repeating the same configuration method for each gateway. A gateway with a built-in SD card slot can save time and frustration in this regard. After setting up the first gateway, the configuration instructions can be automatically stored on the SD card, which can then be used to complete the configuration of the rest of the gateways. The engineer only needs to insert the SD card and turn on the gateway. All the configurations will be set in the new gateway automatically, freeing up valuable time for engineers.
Moxa is a leader in edge connectivity, industrial computing, and network infrastructure solutions for enabling connectivity for the Industrial Internet of Things. With over 30 years of industry experience, Moxa has connected more than 71 million devices worldwide and has a distribution and service network to serve customers in more than 80 countries. |